COSHH Cabinet Regulations: Essential Guide for Workplace Safety 2025
COSHH cabinet regulations apply to all UK businesses handling hazardous substances. These rules protect staff from accidents and injuries when working with dangerous materials.
Why COSHH Storage Matters
Every workplace using chemicals, gases, pesticides or cleaning products must comply with these regulations:
- Legal requirement for all UK businesses
- Prevents workplace accidents
- Protects staff from harmful exposure
- Reduces risk of chemical spills
Key COSHH Cabinet Features
COSHH storage cabinets provide essential protection through:
- Secure lockable doors
- Proper ventilation systems
- Spill containment sumps
- Durable construction
These cabinets appear in multiple workplace settings – laboratories, factories, schools and warehouses all rely on proper COSHH storage.
This guide covers all current COSHH cabinet requirements for 2025. Follow these standards to maintain full compliance and keep your workplace safe from hazardous substance risks.
Understanding COSHH Cabinet Regulations in 2025
COSHH legislation establishes essential workplace safety rules for businesses handling dangerous materials. Proper knowledge of these regulations ensures compliance and staff protection.
What are COSHH regulations?
COSHH regulations form the legal framework protecting workers from health risks caused by hazardous substances. UK law requires employers to control exposure to harmful materials in the workplace.
Materials covered under COSHH include:
- Chemicals and chemical products
- Dusts, fumes, vapours and mists
- Biological agents (bacteria and viruses)
- Gases and nanotechnology
Lead, asbestos and radioactive materials fall under separate regulations, not COSHH. HSE treats regulation breaches as serious offences, with non-compliant businesses facing unlimited fines.
Key regulatory changes for 2025
Important COSHH regulation changes take effect in 2025. HSE will discontinue the COSHH e-tool on 31 January 2025. Complete all assessments before this date, as the system becomes inaccessible afterwards. COSHH Essentials direct advice sheets remain available online.
2025 brings stricter enforcement across all sectors. Businesses must implement enhanced safety measures, including proper storage and disposal procedures for hazardous substances. Annual audits and mandatory employee training on hazardous substance risks become required.
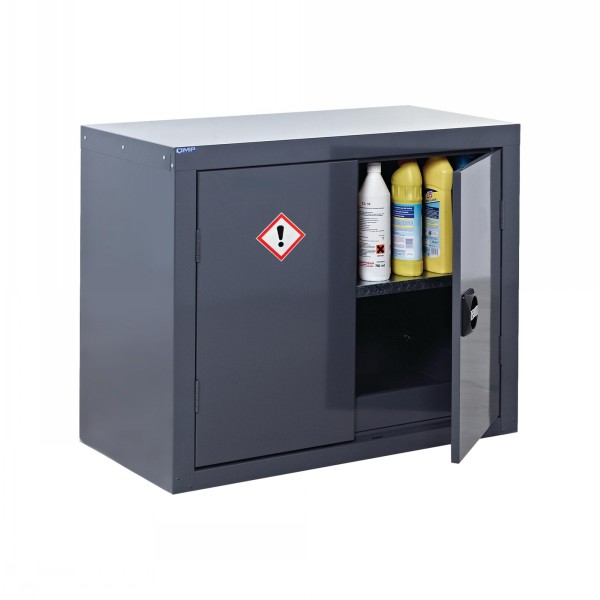
Who enforces COSHH regulations?
HSE holds primary responsibility for COSHH enforcement under the Health and Safety at Work Act 1974. Enforcement duties are split between HSE and local authorities based on workplace type.
HSE directly oversees factories, farms, building sites, mines, schools, hospitals and offshore installations. Local authority environmental health departments handle offices, shops, hotels, restaurants, pubs, museums and care homes.
Both enforcement bodies conduct inspections, issue improvement notices, and prosecute violations. They provide guidance, helping businesses implement proper COSHH storage cabinets and safety measures required for regulatory compliance.
Essential COSHH Cabinet Requirements
Proper storage facilities protect workers from hazardous substances. COSHH cabinets must meet specific standards for maximum safety and full compliance.
Material and Construction Standards
COSHH cabinets need robust construction for daily use and potential incidents:
Cabinet colour coding helps with quick identification:
- Yellow – general hazardous substances
- White – acids and alkalis
- Specific colours for flammable materials
Ventilation Requirements
Ventilation becomes essential when storing substances that emit harmful vapours:
- Mandatory for substances listed in workplace exposure standards
- Indoor storage requires local exhaust ventilation (LEV) where hazard release cannot be eliminated
- Building ventilation needs five to ten air changes per hour
- Mechanical ventilation must keep toxic substance concentration as low as practical
Spill Containment Specifications
All COSHH cabinets must include leak-proof construction:
- The integral sump at the base collects accidental spills
- Sumps must hold 110% of the largest container’s volume
- Adjustable spill-retaining galvanised shelves with raised edges
- Shelves support 50-70kg uniformly distributed load
Locking Mechanisms and Security
Security features prevent unauthorised access:
- High-security seven-lever safe door lock with anti-pick mechanism or 2-point locking system with two keys
- Reinforced doors with five-knuckle hinges and full-length stiffeners
- Secure location away from potential vandalism or arson threats
Only trained personnel should access hazardous substance storage. Cabinets must remain locked when unattended.
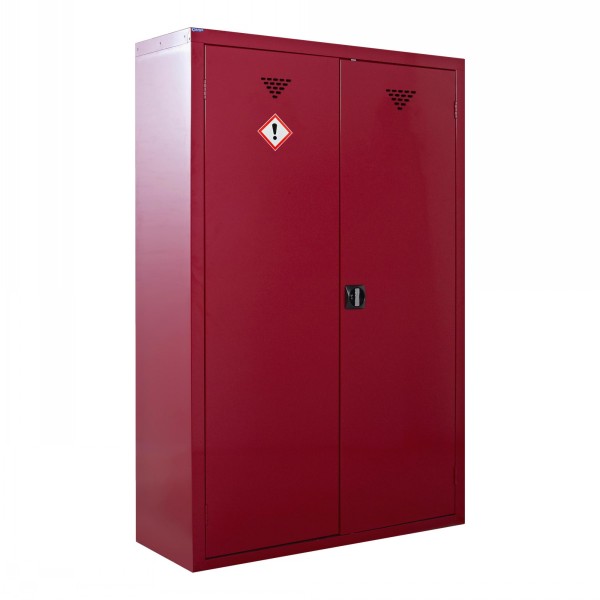
Compliance and Documentation for COSHH Storage
Proper documentation proves compliance with COSHH cabinet regulations. Your business needs complete record-keeping systems to meet regulatory standards.
Required Safety Documentation
All workplaces storing hazardous substances must maintain these essential records:
- Material Safety Data Sheets (MSDS) for all chemicals on site
- Current inventory of all hazardous materials
- Safety procedures for handling and storage
- Employee training records
- Emergency response plans for spillages
- Chemical spill cleanup procedures
MSDS sheets contain critical safety information, including hazard details, handling instructions and emergency protocols. Your hazardous materials inventory serves as a crucial reference for emergency services during incidents.
Risk Assessment Procedures
Risk assessments create the foundation for COSHH compliance. Employers must evaluate hazardous substance risks and implement appropriate controls. Assessments should focus on safe handling, storage and transportation.
Complete risk assessments include:
- Hazard identification
- Evaluation of potential harm and affected persons
- Precautionary measure establishment
- Control measure implementation
- Regular effectiveness reviews
Businesses with five or more employees must record all significant findings – this is a legal requirement.
Inspection and Maintenance Records
Regular checks keep COSHH storage cabinets fit for purpose. Cabinets storing flammable liquids need comprehensive annual inspections for function and reliability. Document all inspections in writing.
Your maintenance records must show:
- Inspection and maintenance dates
- Names of qualified inspection personnel
- Identified faults and completed repairs
- Ventilation system testing results (required every 14 months)
Thorough documentation provides compliance evidence during audits while maintaining workplace safety standards.
Industry-Specific COSHH Storage Regulations
Different industries face unique hazardous substance challenges. Specific storage requirements exist beyond general regulations to ensure maximum safety across varied work environments.
Healthcare Sector Requirements
Healthcare facilities need specialised COSHH storage solutions:
- Strict regulatory compliance beyond basic COSHH guidelines
- Enhanced security for controlled substances
- Clean-setting compatible cabinets
- Integration with pharmaceutical management systems
Healthcare COSHH cabinets typically feature antimicrobial coatings. Strategic placement balances security needs with emergency access requirements.
Manufacturing Industry Standards
Manufacturing environments handle different storage challenges:
- Larger volumes of fewer hazardous materials
- Need for industrial-grade cabinet construction
- Robust construction standards for harsh environments
- Higher throughput access requirements
Manufacturing COSHH storage must balance centralised stores versus point-of-use access. Proper integration with production workflows maintains efficiency without compromising safety standards.
Laboratory and Research Facility Regulations
Laboratories present distinct storage requirements:
- Management of diverse chemicals in smaller quantities
- Frequent access needs for multiple users
- Under-bench installation for point-of-use access
- Compact cabinet designs for space-limited environments
Biological agents need special attention with classification into four hazard groups (HG1-HG4). First-time use of biological agents classified as HG2, HG3 or HG4 requires HSE notification.
Construction Site Compliance
Construction sites must address outdoor storage challenges:
- Dedicated chemical stores away from high-traffic zones
- Separation from potential ignition sources
- Weather protection for all storage units
- Emergency service accessibility
Construction COSHH cabinets need secure locking to prevent vandalism. Site owners remain responsible for any contamination regardless of unauthorised access, making spill response protocols essential.
Conclusion
Proper COSHH cabinet implementation creates safer workplaces across UK businesses. These regulations protect staff and ensure legal compliance despite their initial complexity.
Safety begins with selecting appropriate storage cabinets that meet:
- Material construction standards
- Ventilation requirements
- Security specifications
Thorough documentation proves essential for regulatory adherence:
- Complete risk assessments
- Updated inspection records
- Clear safety procedures
- Staff training documentation
Different sectors face unique COSHH challenges. Healthcare facilities, manufacturing plants, laboratories and construction sites each need tailored solutions balancing accessibility with security.
Successful compliance requires:
- Regular review of safety protocols
- Scheduled storage system assessments
- Current staff training on safety guidelines
Careful attention to these requirements creates safer workplaces while avoiding non-compliance penalties. COSHH cabinet regulations might seem demanding, but they serve one vital purpose – protecting your workforce from hazardous substance risks.
Frequently asked questions about COSHH cabinets.
Where should COSHH cabinets be located in the workplace?
COSHH cabinets should be placed in areas with clear exits and near washing facilities. They should be easily accessible yet secure, away from high-traffic zones and potential ignition sources. The specific location may vary depending on the industry and workplace layout.
How often should COSHH training be conducted?
While there’s no legal expiry date for COSHH training, it’s recommended to provide regular refresher courses. The frequency depends on factors such as the nature of the business, types of hazardous substances used, and level of risk involved. Many employers opt for annual training to maintain awareness and reinforce best practises.
What are the key components of a COSHH risk assessment?
A thorough COSHH risk assessment should include identification of potential hazards, evaluation of who might be harmed and how, establishment of precautionary measures, implementation of control measures, and regular review of the assessment’s effectiveness. For businesses with five or more employees, recording significant findings is a legal requirement.
What are the essential features of a COSHH storage cabinet?
COSHH storage cabinets must have robust construction, typically using heavy-duty steel. They should feature leak-proof design with an integral sump for spill containment, proper ventilation systems, secure locking mechanisms, and colour coding for easy identification of contents. The cabinets should also meet specific fire safety standards.
How do COSHH regulations differ across industries?
COSHH regulations are tailored to address unique challenges in different sectors. For instance, healthcare facilities require enhanced security for controlled substances, manufacturing environments need industrial-grade cabinets for larger volumes, laboratories often use compact designs for diverse chemicals, and construction sites must consider outdoor storage challenges. Each industry must comply with general COSHH guidelines while addressing sector-specific requirements.
What is considered a ‘safety risk’ when storing hazardous substances?
A safety risk in chemical storage arises when dangerous substances are improperly handled or stored, potentially leading to fires, spills, toxic exposure, or contamination. Poor ventilation, unsecured cabinets, or mixing incompatible substances can increase the risk of incidents. COSHH-compliant storage helps minimise these dangers through structured, secure practices.
What are the rules around the safe storage of flammable substances?
Flammable substances must be kept in clearly labelled, fire-resistant COSHH cabinets located away from heat sources, ignition points, or direct sunlight. These cabinets should feature spill-proof sumps and proper ventilation. Always refer to the hazard symbols on product labels to determine the right containment approach and separation from other hazardous liquids.
How can I identify substances hazardous to health in my workplace?
Any material carrying COSHH hazard symbols – such as corrosive, toxic, or flammable – should be flagged as a substance hazardous to health. Consult the product’s safety data sheet (SDS) to understand potential risks. Common hazardous substances include cleaning agents, industrial chemicals, solvents, paints, and dusts generated from work processes.
What’s the best approach for the secure storage of hazardous chemicals?
Secure storage means keeping hazardous chemicals in lockable, steel COSHH cabinets with reinforced doors and sumps to catch spills. Store incompatible materials separately and ensure access is restricted to trained personnel. Cabinets should also be positioned in low-risk areas—well away from emergency exits, public walkways, or ignition sources.
Why is understanding the Control of Substances Hazardous to Health regulations important?
Knowing the Control of Substances Hazardous to Health (COSHH) regulations is vital for preventing accidents, reducing risks to health, and complying with UK law. These rules guide employers on assessing, controlling, and storing hazardous substances safely. Failure to comply can result in injury, illness, or prosecution.
What types of substances fall under COSHH regulations?
A wide range of materials are governed by COSHH, including cleaning products, adhesives, paints, solvents, lab reagents, and even some natural materials like dust and mould. If a substance can cause skin irritation, respiratory problems, or other health effects, it must be managed under COSHH.
What are the hazards of storing chemicals incorrectly?
Improper storage of chemicals can lead to spills, fires, toxic exposure, or chemical reactions. For example, storing dangerous substances like acids and alkalis together may cause heat and gas release. Without appropriate containment, such accidents pose a major threat to worker health and site safety.