Used Pallet Racking: What Buyers Must Know Before Purchase
Used pallet racking delivers immediate cost savings of 30-50% compared to new systems. Warehouse managers working with tight budgets find second-hand pallet racking an effective storage solution.
- True cost implications
- Safety standard requirements
- Structural integrity assessment
- Compliance verification
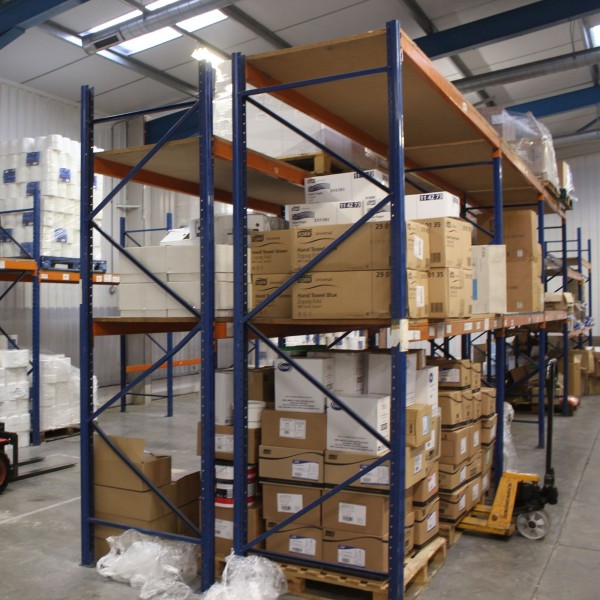
Pros and Cons of Buying Used Pallet Racking
Cost savings vs. long-term reliability
- Save 30-50% compared to new systems
- Reduce upfront investment costs
- Access quality storage at fraction of new prices
Reliability concerns:
- No manufacturer warranties
- Absence of guarantee transfers all maintenance costs to your business
- Hidden expenses include compliance retrofitting, component replacement, and engineering certifications
Quick availability vs. limited customisation
- Immediate availability eliminates manufacturing delays
- Rapid deployment for urgent storage needs
- Ideal for temporary warehouse transitions and seasonal inventory fluctuations
Customisation limitations:
- Warehouse layout must accommodate available racking
- Compatible components may be difficult to source
- Future expansion plans become complicated
- System design optimisation becomes restricted
Sustainability benefits vs. unknown history
- Extends product lifecycles
- Reduces manufacturing demand
- Decreases resource consumption and energy usage
- Supports sustainability initiatives
History uncertainties:
- Previous usage patterns remain undocumented
- Weather exposure may cause hidden corrosion
- Maintenance records often unavailable
- Structural stresses cannot be verified
Undocumented damage or stress in Second Hand Racking
Used pallet racking inherits all previous damage from material handling equipment. Most damage remains invisible to untrained eyes. One expert explains: buying used racking equals “buying a used car; you don’t know where it has been and what issues have occurred with it.”
Missing or incompatible parts
- Loose or improvised connections
- Broken planks and missing support blocks
- Poorly welded beams or bent diagonals
- Rusted or corroded components
No warranty or after-sales support
Most used pallet racking comes without manufacturer warranties. Your business bears full responsibility for failures or maintenance requirements. This absence of guarantee can negate initial cost savings.
Ensuring Safety and Legal Compliance
SEMA-approved inspections requirements
SEMA (Storage Equipment Manufacturers’ Association) inspections provide the UK safety standard for warehouse racking. These inspections verify that second-hand racking meets load-bearing capacities and stability requirements.
SEMA-approved inspections identify potential hazards early, preventing accidents and maintaining productivity. Regular inspections ensure compliance with Health and Safety regulations.
- Daily visual checks by staff for obvious damage
- Weekly or monthly checks by trained personnel
- Annual inspections by SEMA-approved competent person
Verifying load ratings and structural integrity
- Check all racks display visible SWL (Safe Working Load) labels and Load Notices
- Request original manufacturer specifications from seller
- Inspect for overloading signs – sagging beams or deformed base plates
- Test stability by assembling a small section before purchase
Legal consequences of non-compliant racking
UK used pallet racking must comply with the Health and Safety at Work Act 1974 and PUWER (Provision and Use of Work Equipment Regulations).
- Unlimited fines and prosecution
- Workplace injury compensation claims
- HSE enforcement notices shutting down warehouses
- Increased insurance premiums
Recent case: Logistics company fined £500,000 after worker injury from collapsing racking system not inspected for over a year.
Making the Right Purchase Decision
Your warehouse needs and business circumstances determine the best choice between new and second hand pallet racking. Critical factors require careful evaluation before purchase.
Compare used vs. new based on your business goals
Operational priorities guide your decision:
Budget considerations: Used systems cost 30-50% less than new. Limited capital makes used racking ideal for budget-conscious operations.
Timeline requirements: Second hand racking offers immediate availability. New systems involve manufacturing delays that could impact your project.
Get expert advice before buying
- Professional inspection identifies critical damage like deformations or pitted rust
- Racking engineers ensure relocating used systems follows proper certification processes
- Building code review verifies local regulation compliance
Check used pallet racking for sale near you
Local supplier selection requires specific criteria:
• Choose warehouse racking specialists over general resellers
• Visit facilities for physical material inspection
• Quality suppliers welcome pre-purchase visits and inspections
Understand used pallet racking prices and value
Price considerations extend beyond initial cost:
• Condition, brand, and configuration affect pricing
• Lowest price doesn’t guarantee best value
- Uniform distributed load (UDL) capacity
- Maintenance history records
- SEMA guideline compliance verification
- Beam lock inclusion confirmation
Conclusion
Second-hand pallet racking delivers cost advantages for warehouse managers with budget constraints. Balance these savings against safety risks and long-term reliability concerns. Professional inspection identifies hidden damage before purchase.
- Short-term projects: Second-hand options provide immediate availability
- Permanent installations: New systems offer better customisation
- Tight budgets: Used racking reduces upfront costs
- Precise specifications: New systems deliver exact requirements
Quality creates safety. Proper assessment, professional guidance, and thorough inspection make second hand systems viable storage solutions. The right approach balances cost efficiency with operational safety requirements.